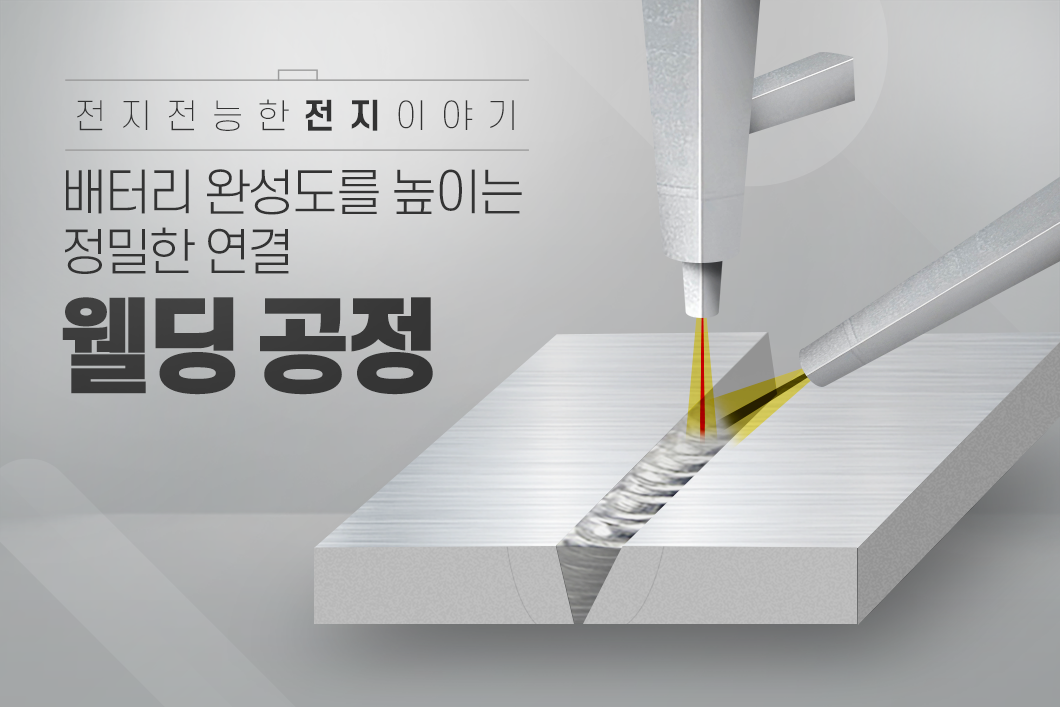
수백 개의 셀(Cell)이 연결되어 하나의 모듈(Module)을 이루고, 여러 모듈이 모여 팩(Pack)이 되면 비로소 전기차나 ESS(에너지저장장치) 등에 탑재됩니다. 이처럼 각 단계가 전기적으로 정확히 연결되어야만 배터리로서의 역할을 수행할 수 있는데요. 배터리의 다양한 구성 요소들을 하나로 연결하는 과정을 바로 ‘웰딩(Welding) 공정’이라고 합니다. 웰딩 공정은 배터리의 성능과 품질에 큰 영향을 미치는 중요한 공정인데요. 그렇다면 웰딩 공정에는 어떤 종류가 있고, 각각의 용접 방식은 어떤 특징을 가질까요? 지금부터 하나씩 살펴보겠습니다.
배터리 제조의 숨은 핵심, 웰딩(Welding) 공정
웰딩(Welding)이란, 두 개 이상의 금속이나 소재를 열이나 압력을 이용해 강하게 접합하는 용접 기술로, 배터리 제조에서 매우 중요한 역할을 합니다. 배터리 셀 간 전기적 연결을 위해 전극과 탭(Tab) 사이를 정밀하게 접합할 때, 그리고 모듈(Module) 단위의 조립 과정에서도 ‘버스 바(Bus Bar)’와 같은 전기적 연결 부품을 결합할 때 웰딩 기술은 필수적으로 활용됩니다.
배터리 제조에서 웰딩은 단순한 접합을 넘어, 전기 전도성과 기계적 강도를 모두 만족시켜야 합니다. 그만큼 고도의 기술이 요구되는데요. 특히 배터리 탭에 주로 사용되는 구리(Cu)와 알루미늄(Al)처럼, 성질이 서로 다른 소재를 접합할 경우 녹는점, 열팽창률, 열전도도 등의 차이로 인해 접합 품질을 확보하기가 까다로워 매우 정밀한 기술이 필요합니다. 따라서, 소재 특성에 최적화된 용접 방식을 선택하는 것은 배터리 성능과 안전성에 중요한 영향을 미칩니다.
정밀한 전류 제어로 접합하는, 저항 용접(Resistance Welding)
저항 용접(Resistance Welding)이란, 전류를 흘려 저항에 의해 발생하는 열로 접합 부위를 녹여, 두 금속을 접합하는 용접 기술입니다. 두 금속 판을 전극 사이에 넣고 압력을 가한 상태에서 짧은 시간 동안 강한 전류를 흘리면, 접촉면에 저항열이 발생하게 되는데요. 이 과정에서 접합 부위가 집중된 열로 인해 국부적1으로 용융2되어 두 금속이 강하게 결합되는 원리입니다.

가장 대표적인 저항 용접은 ‘저항 점용접(RSW, Resistance Spot Welding)’으로, 이름 그대로 좁은 면적에 집중된 점(spot)을 만들어 저항 용접의 원리를 적용하는 방식입니다. 이 방법은 접합 부위가 매우 좁기 때문에, 정밀한 부품 접합이나 박막 금속을 다루는 공정에 적합합니다.
또한 저항 용접을 활용하면 같은 부품을 반복적으로 용접해야 하는 대량 생산 시스템에서도 안정적인 품질을 유지할 수 있습니다. 짧은 시간 동안 흐르는 전류를 활용해 순간적으로 접합이 이루어지기 때문입니다. 아울러 저항 용접은 모니터링을 통한 정밀한 열 제어가 가능해 자동화 시스템에 적합하고, 공정 중 스패터(Spatter)나 흄(Fume)과 같은 유해 물질 발생이 적어 작업 환경이 안전하다는 장점도 있어, 다양한 제조 분야에서 활용되고 있습니다. 특히 원통형 배터리 제조에서는 원통형 케이스의 내부 바닥 면과 음극 탭(Negative Tab)을 접합하는데 주요 방식으로 사용됩니다.
다만, 저항 용접은 많은 전류가 필요하기 때문에 규모가 큰 전력 설비를 필요로 합니다. 또한 전류나 가압력, 용접재의 재질과 두께 등에 따라 용접 조건이 달라지기 때문에, 최적의 용접 조건을 선정하기도 쉽지 않죠. 접합 상태를 외관만으로 판정하기 어렵고, 비파괴 검사법3이 부족해 내부 결함을 파악하기 힘든 점도 한계로 꼽히고 있습니다.
다양한 소재를 접합하는, 초음파 용접(Ultrasonic Welding)
초음파 용접(Ultrasonic Welding)은 초당 20kHz상의 고주파 진동 에너지를 이용하여, 동일한 금속 또는 서로 다른 종류의 금속을 접합하는 기술입니다. 이 방식은 두 재료를 맞댄 상태에서 초음파 진동을 가해 국부적으로 발생하는 열과 소성 변형을 활용하는데요. 이를 통해 접촉면의 산화막이나 오염층이 제거되면서 고상 접합4이 일어나, 용융 없이도 재료의 강한 결합이 형성되는 원리입니다.


초음파 용접은 성질이 서로 다른 금속부터 고분자 물질, 필름 같은 얇은 재료까지 다양한 소재를 접합할 수 있는 기술입니다. 이 방식은 저항 용접처럼 전류를 직접 흘려 열을 발생시키는 방식이 아니기 때문에, 전기적 열 손실이 없고 용접 부위의 온도가 비교적 낮아 열에 민감한 재료에도 적용이 가능하죠.
초음파 용접은 항공우주와 자동차 산업에서 특히 주목받고 있는데요. 다양한 모빌리티에서 경량화, 고성능 소재가 널리 활용되면서, 서로 다른 물질 간의 정밀한 접합이 중요해지고 있기 때문입니다. 초음파 용접은 열영향부 없이 용접 가능하며, 소재 간 녹는점의 차이에 덜 민감하기 때문에 여러 소재를 결합하는 하이브리드 접합기술로 크게 주목받고 있습니다.
이차전지 제조공정 전반에 확대되는, 레이저 용접(Laser Welding)
레이저 용접(Laser Welding)이란, 고밀도의 에너지 빔을 이용해 재료를 순간적으로 녹여 접합하는 용접법입니다. 높은 밀도의 에너지 빔이 접합 부위에 깊게 침투해, 폭이 좁고 깊은 부위의 접합에 알맞은 기술이죠.
이러한 특징은 열영향부(HAZ: Heat Affected Zone)과 용접부 주변의 열 변형을 최소화하는데 효과적입니다. 또한, 깊은 침투는 두께가 서로 다른 재료의 용접에도 적합하며, 접합 부위가 많은 경우에도 안정적인 용접이 가능하죠.
한편, 반사율이 높은 금속을 용접할 경우, 반사광이 장비에 손상을 줄 수 있어, 광학계5를 일정 각도로 기울여 빔을 조사하는 방식이 사용되기도 합니다.

레이저 용접은 이차전지 제조 공정 전반에 걸쳐 활발히 활용되고 있습니다. 기존의 저항 용접이나 초음파 용접과 같은 ‘접촉식’ 방식은 전극이나 진동자(혼, Horn)가 재료 표면에 직접 닿아야 하는데요. 이 때문에 툴 마모나 접합부 변형, 소음 및 분진, 설계 제약 등의 한계가 있었습니다.
반면, 레이저 용접은 ‘비접촉식’ 공정으로, 셀 표면에 맞닿을 필요가 없고 제약이 적어, 원통형, 각형, 파우치형 등 다양한 형태의 배터리 셀에 유연하게 적용할 수 있죠. 이러한 특징 덕분에 레이저 용접은 셀 내부 전극 접합부터 셀 간 전기적 연결을 수행하는 모듈 및 팩 공정, 그리고 BMS 연결 단계까지 폭넓게 적용되고 있습니다.

최근 전기차 주행거리 향상을 위해 고용량 배터리 개발이 가속화되면서, 에너지 밀도를 높이기 위해 극판과 탭 적층 수가 증가하는 추세인데요. 이에 따라 다적층 구조를 안정적으로 접합할 수 있는 고정밀 레이저 용접 기술의 수요도 함께 증가하고 있습니다.
한눈에 비교하는 웰딩 공정

배터리 성능이 향상을 거듭하면서 소재는 더 다양해지고, 제조 과정도 고도화되고 있습니다. 이에 따라 배터리 내부 부품을 연결하는 웰딩 공정 역시 자동화 시스템, 실시간 품질 모니터링, 비파괴 검사 등 첨단 기술과의 융합을 통해 빠르게 진화하고 있는데요. 앞으로도 웰딩 공정의 혁신이 배터리 제조 경쟁력의 중요한 열쇠가 될 것으로 보입니다.