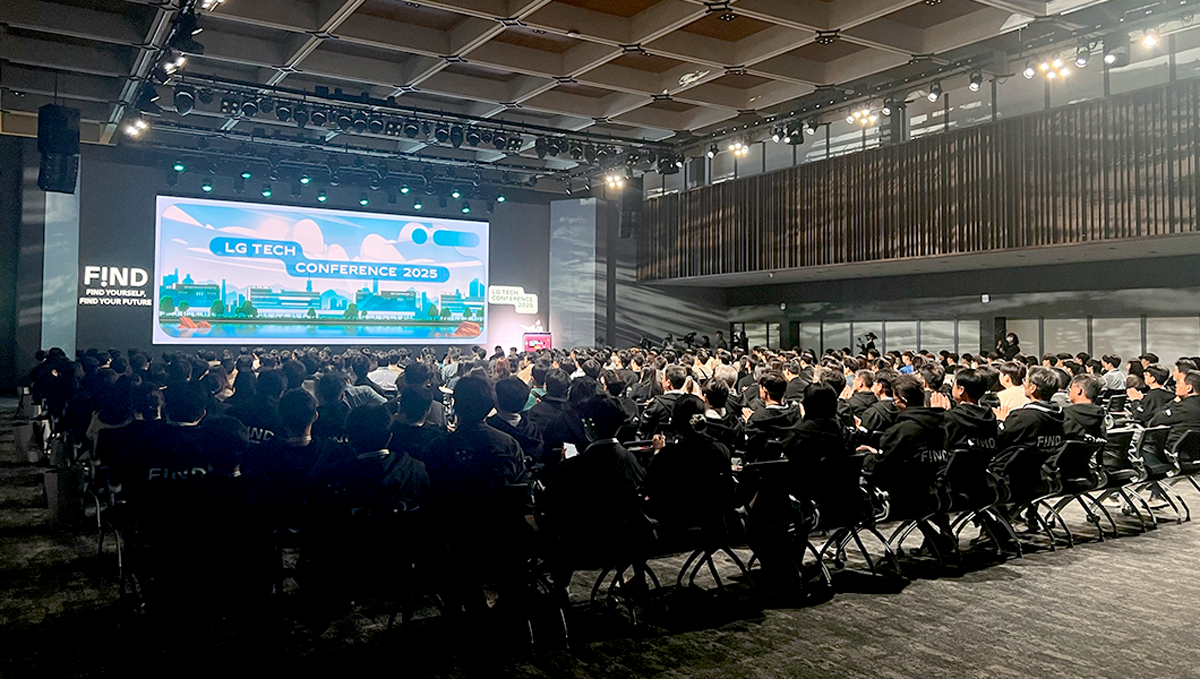
With the rapid growth of the e-mobility industry, powered by the increasing popularity of electric vehicles (EVs) and e-bikes, customer demands for batteries are becoming more sophisticated. Beyond competing on core performance metrics such as driving range and output, battery makers are now focusing on development capabilities that address hidden needs, including AI-driven battery management systems and next-generation safety-enhanced batteries. In response, LG Energy Solution is delivering exceptional performance by introducing innovation in its manufacturing process, while also developing next-generation battery technologies.
The LG Tech Conference 2025, held at LG Science Park on April 3, aimed to showcase such technological innovations and future visions. Leading researchers from LG affiliates shared their hands-on research experiences and results at the venue. Representing LG Energy Solution, Jung-hoon Lee of the Advanced Cell Research Group presented a technology roadmap for EV batteries under the theme “LG Energy Solution’s Advanced EV Cell Development Strategy to Prepare for Future Mobility,” introducing key technologies shaping the future of the EV industry as well as the company’s strategic direction. Here is a closer look at how he presented LG Energy Solution’s vision for future EV battery technology!
LG Energy Solution’s EV Battery Technology Roadmap
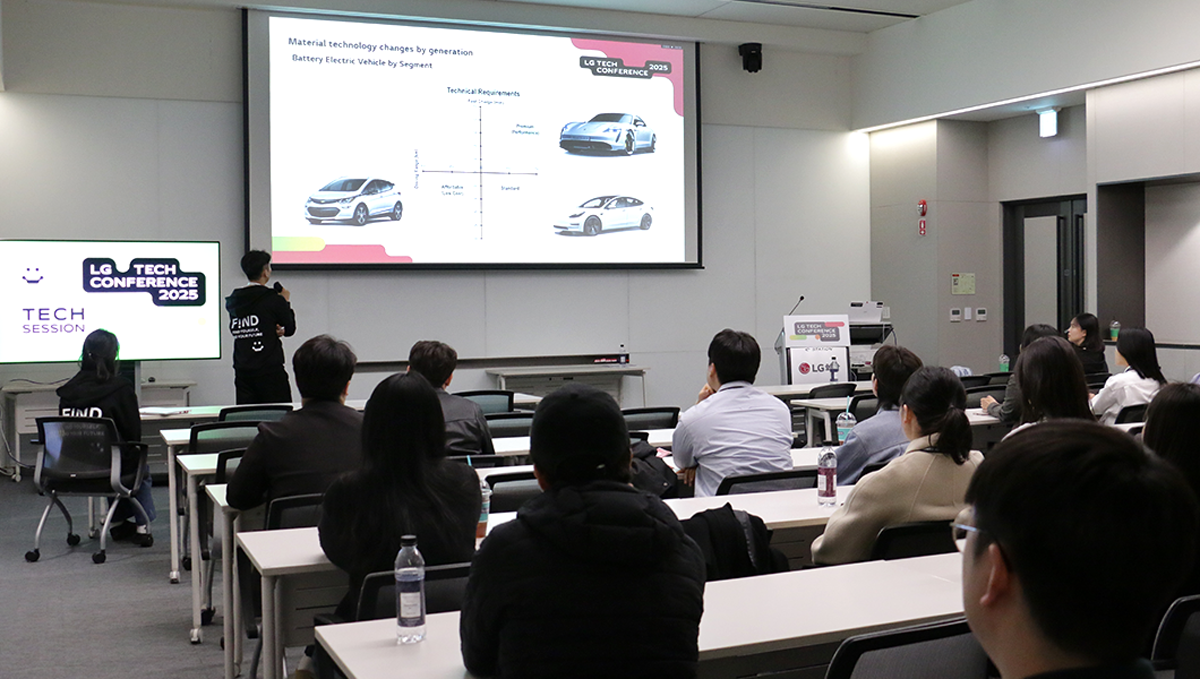
LG Energy Solution is leading innovation in battery technology by developing cutting-edge batteries for diverse applications, including Energy Storage Systems (ESS), Urban Air Mobility (UAM), and Backup Battery Units (BBU). Among these, EV batteries are categorized into three segments – Premium, Standard, Affordable – according to the company’s technology roadmap. These segments are distinguished by four key criteria: driving range, charging time (including fast charging), cost, and energy density.
Of the three, Premium batteries focus on high performance. High-nickel cathodes are used to enhance energy density and capacity, while research on silicon anodes, a key component of next-generation batteries, is ongoing to support fast charging and longer driving range.
For Standard batteries, the strategy is to lower costs while securing stability by using mid-nickel batteries with a nickel content reduced to 60-70%. To further extend driving range even with the lower nickel content, LG Energy Solution is dedicated to increasing voltage and thereby elevating energy density. Additional goals include decreasing cost by developing innovative technologies to remove active materials in the manufacturing process, and achieving price competitiveness with internal combustion engine vehicles by 2027.
Affordable batteries are equipped with lithium ferro-phosphate (LFP) cathodes. While LFP offers greater price competitiveness and stability than nickel-cobalt-manganese (NCM), it lags behind in energy density and fast charging. The company plans to deliver high performance and safety at reasonable prices through its differentiated “Dry electrode process.”
[Premium Segment] The Evolution of Advanced NCM Cathode Technology
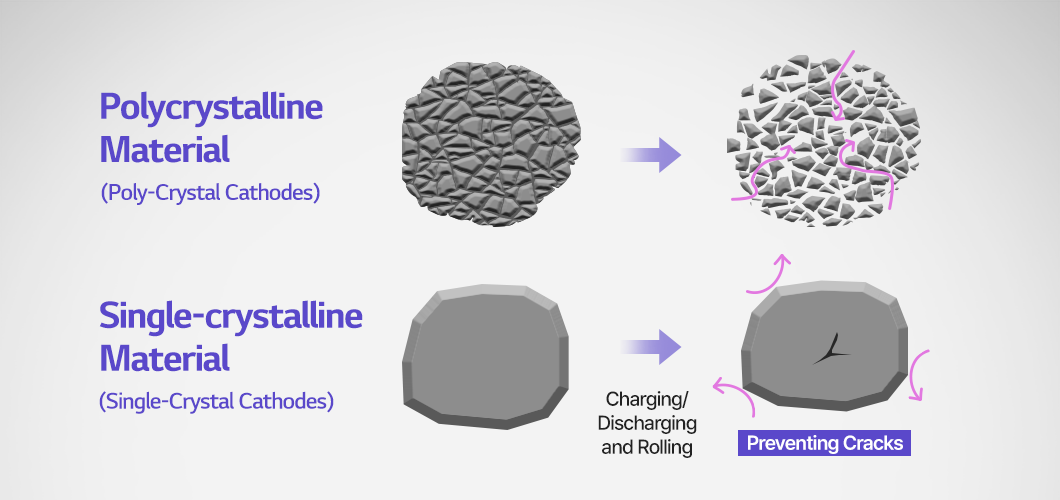
Nickel-cobalt-manganese (NCM), one of the most common cathode materials, is essential for high-performance EV batteries. LG Energy Solution has continued to explore various methods to maximize the advantages of NCM cathodes.
A notable example is single-crystal (SC) cathode material research. The conventionally used polycrystalline (PC) structures consist of multiple interconnected crystals, and therefore can cause intergranular cracking during charging, discharging or compression, negatively affecting battery performance. In contrast, the SC structure, consisting of a single crystal, mitigates this risk, resulting in higher stability and longer battery life.
Along with that, the company is intensifying its efforts in multi-doping1 optimization and surface coating technology to suppress phase transitions2 and enhance surface stability.
It is also working on techniques for thinner and more uniform wrapping of cathode particles. Further advancing this technology will allow higher nickel content in battery materials. Since higher nickel content increases energy density, it extends the driving range of EVs. A longer driving range helps decrease the relative cost of driving EVs, lowering the total cost per distance traveled, ultimately offering greater value to customers.
[Premium Segment] Innovating Anode Materials with Silicon
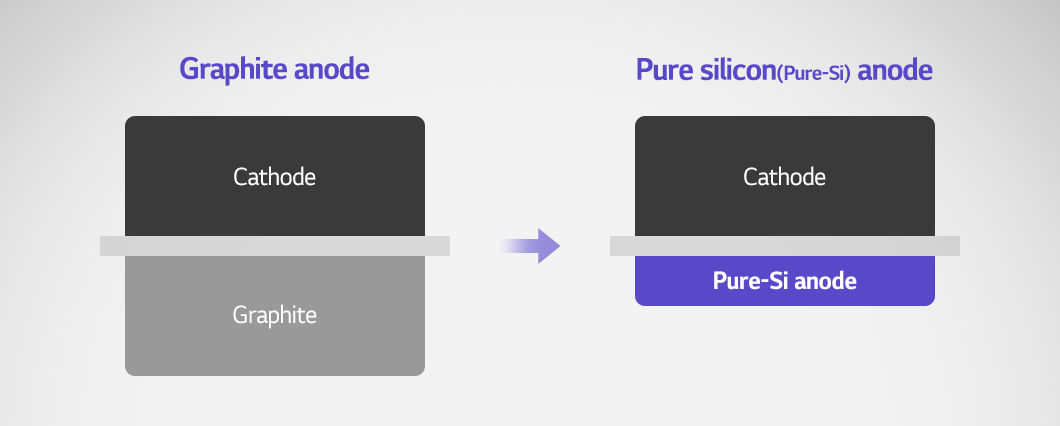
As mentioned earlier, the key to Premium batteries is high performance, and enabling fast charging through the anode is essential for their production. One way to achieve fast charging is to make the anode thinner, allowing current to flow quickly. For this reason, silicon, which has a higher energy storage capacity than the commonly used graphite, is considered a next-generation anode material.
However, silicon has a physical limitation: it expands and contracts during charging and discharging. To address this volume change, LG Energy Solution adopted silicon oxide (SiOx) as the strategy for its first-generation models. Silicon anode materials are not used independently but are combined with other materials to achieve better performance. They are classified into silicon oxide and silicon carbide (Si-C) depending on the structure of the combination. Silicon oxide works as a buffer that mitigates the expansion of silicon, but has a lower capacity than Si-C, which can degrade the battery’s overall performance. To overcome this limitation, researchers have added small amounts of metal to improve performance.
The second-generation strategy is to adopt Silicon/Carbon (Si/C) composites. While this material offers the high capacity of silicon and the stability of carbon, it is extremely difficult to manufacture. Although once considered commercially unviable, LG Energy Solution has almost completed its development through continuous challenges and technological innovation.
LG Energy Solution’s ultimate goal is to apply pure silicon to the anode. The company continues its research into various methods, as a pure-silicon anode offers higher capacity and potential cost reduction.
[Premium Segment] Enhancing Stability with LG Energy Solution’s SRS®
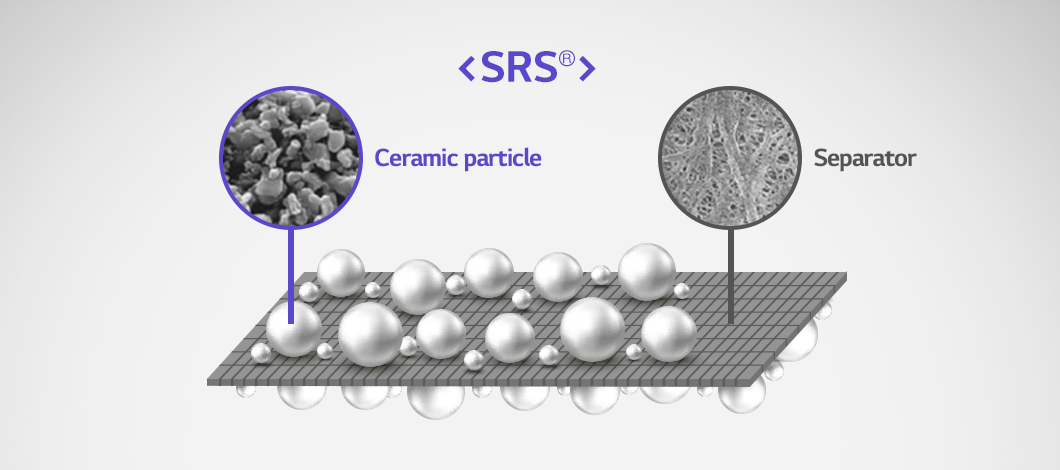
To further enhance the safety of high-capacity, high-output Premium batteries, LG Energy Solution developed Safety Reinforced Separator (SRS®), a safety-focused solution. The first-generation SRS®, released in 2024, was produced by applying a ceramic coating to conventional separators. This design provides a dual safety mechanism: it shuts down3 the micropores, transport pathways for lithium ions, during abnormal battery operation to mitigate potential risks; and it helps the separator to retain its shape without shrinking in high-temperature environments, to prevent short circuits between electrodes4.
In the second-generation SRS®, the ceramic-coated layer became significantly thinner, indicating that the company is capable of controlling the thickness of the coating. This thin and uniform coating has improved manufacturing efficiency and production speed, enhancing the battery’s price competitiveness and energy density, ultimately contributing to longer driving range.
The third-generation SRS® is being developed with the goal of improving performance, particularly in durability and output. The company is also conducting research on environmentally friendly separator materials and technologies including PFAS5-free binder coating and aqueous coating methods.
[Standard Segment] Improving Safety and Affordability with the Development of Mid-nickel Materials
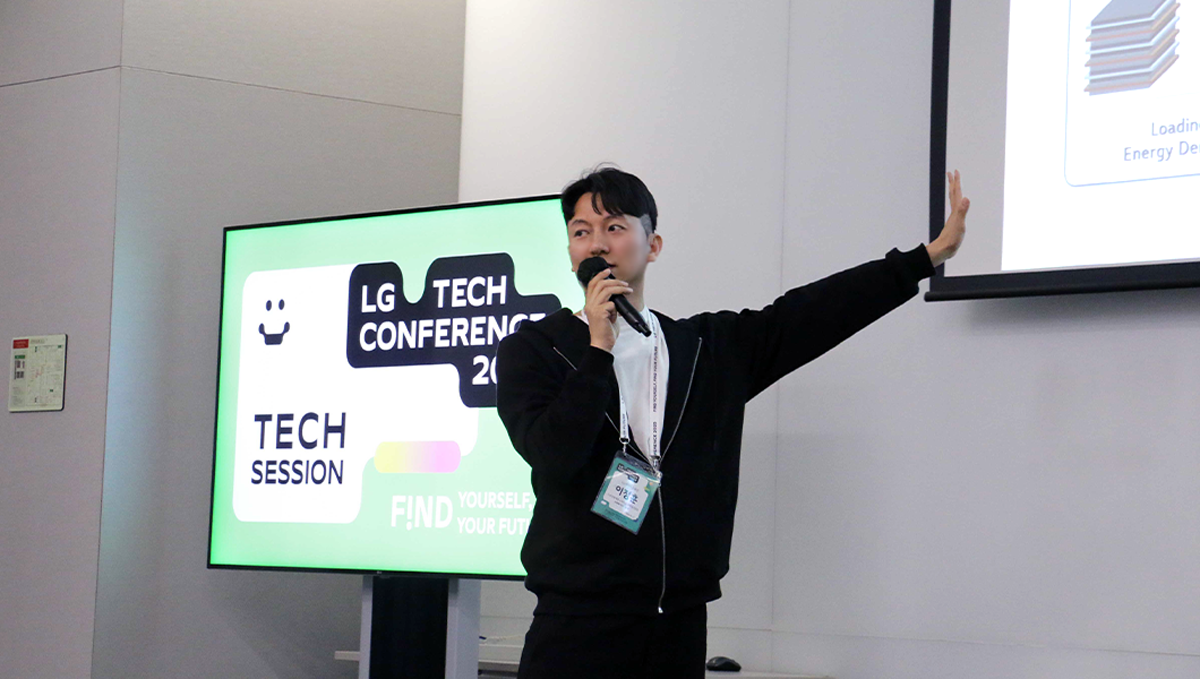
For its Standard batteries, LG Energy Solution’s strategy is to lower cost by decreasing nickel content while securing stability. One of the key materials under research is mid-nickel, which has a lower proportion of nickel.
The company addressed the drop in energy density and durability resulting from lower nickel content by increasing voltage. High-voltage mid-nickel batteries can store more energy and provide more power, thereby extending driving range. In addition, reducing nickel content and raising the proportion of manganese and cobalt helps improve stability.
Furthermore, LG Energy Solution is developing core technologies to reduce cathode material cost, with the aim of bringing EV prices closer to those of internal combustion engine vehicles. When completed, this development is expected to mark a turning point in popularizing EVs.
Along with material development, the company is strengthening its capabilities in AI-driven materials research. Developing cathode materials requires evaluating numerous material structures, but testing each one is time- and resource-intensive. However, Materials Informatics (MI)6 and AI-driven technologies can deliver quick results and speed up the development process. LG Energy Solution is accelerating development of cathode material by collaborating with AI experts across the LG Group.
[Standard Segment] Enhancing Durability through Additive and Solvent Development
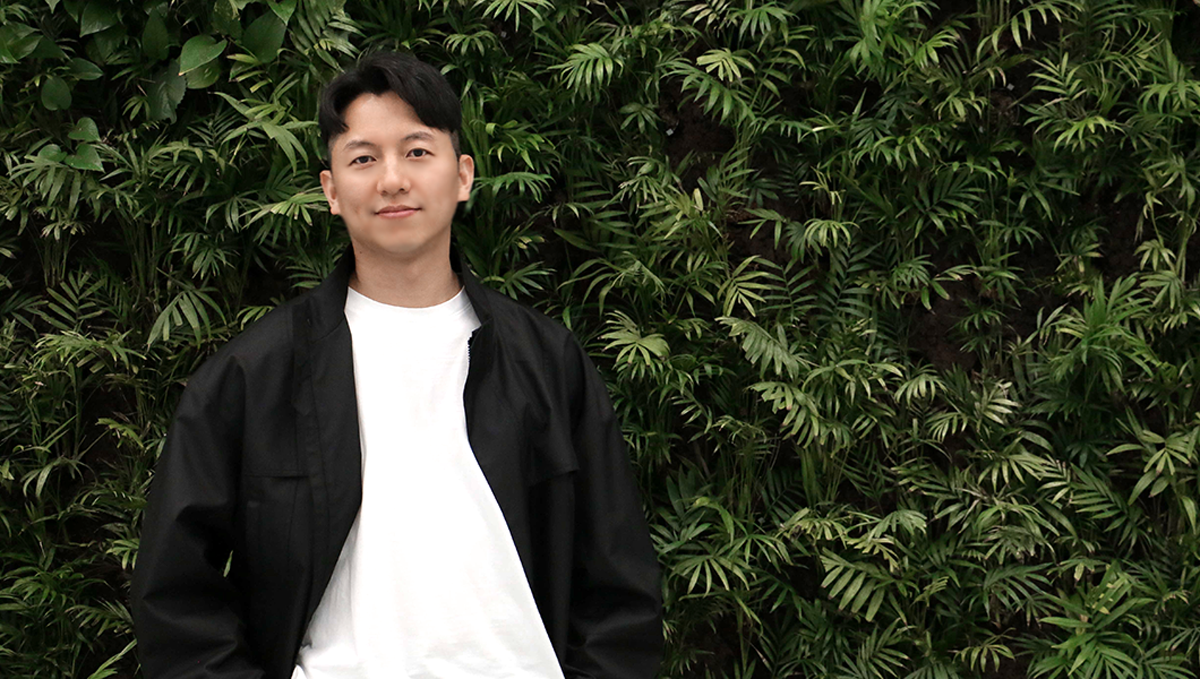
Standard batteries have higher voltages than Premium and Affordable batteries. LG Energy Solution is researching multiple technologies to enhance durability while preventing the increase in reactivity between the anode and electrolyte even in high-voltage environments.
First, the company is focusing on solvent development to reduce the anode’s reactivity with the electrolyte. Solvents support interaction between the anode and electrolyte and enable stable dissolution of electrolyte components. Carbonate-based solvents, commonly adopted for lithium-ion batteries, may generate gas during electrochemical reactions due to their unique structure. To secure battery durability and stability, the company is eliminating gas-forming components from the solvent’s molecular structure and developing more decomposition-resistant solvents.
In addition, the company is proactively adopting AI- and data-driven (DX) technologies in its electrolyte material development efforts. It is committed to maximizing efficiency by building a system that rapidly identifies optimum electrolyte material combinations based on a database containing hundreds of millions of material records.
Lastly, the company is formulating functional additives to protect the silicon anode, which may react with the electrolyte during charging and discharging. These additives work as a protective layer, coating the electrode surface stably and flexibly.
[Affordable Segment] Evolving Manufacturing with the Dry Electrode Process
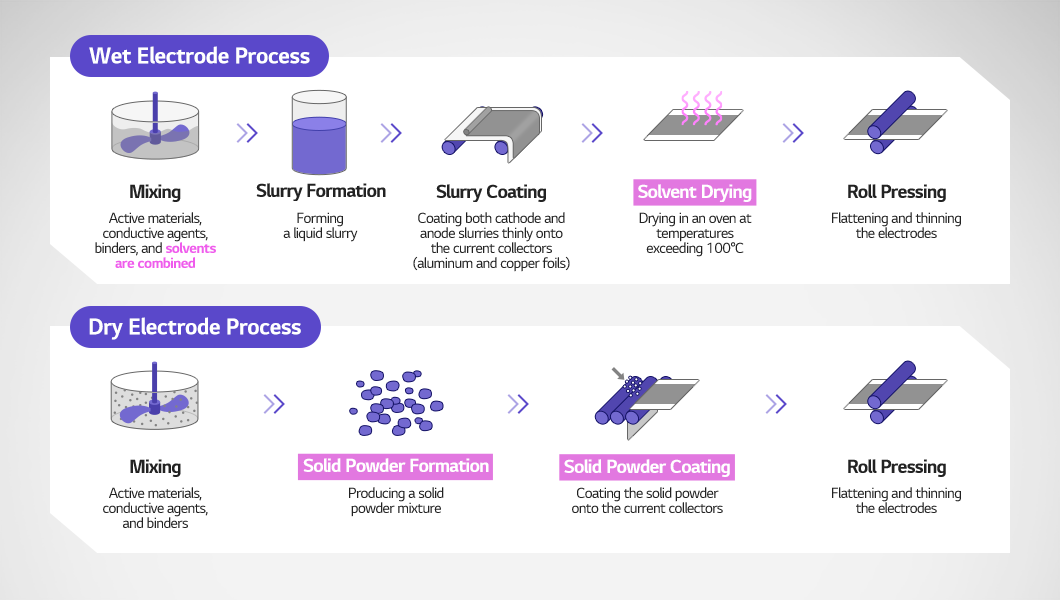
In the Affordable segment, the dry electrode process is gaining significant attention. LG Energy Solution is researching the technology with the goal of rapid commercialization.
The conventional wet electrode process involves dispersing and dissolving raw materials in a solvent, applying the mixture onto a current collector, and then drying it to form an electrode. In contrast, the dry electrode process involves mixing active materials, conductive agents, and binders into a solid powder and coating it onto a current collector without using any solvent. This simplified process further improves production efficiency.
The biggest advantage of the dry electrode process is its ability to maximize “loading” – that is, it allows more active material within the same area, resulting in higher energy capacity and density. In addition, this process is environmentally friendly, as it eliminates the use of solvents and reduces manufacturing costs and power consumption by removing the need for drying equipment and solvent recovery systems.
The Power of LG Energy Solution’s R&D: Data-driven Prediction and Production Automation
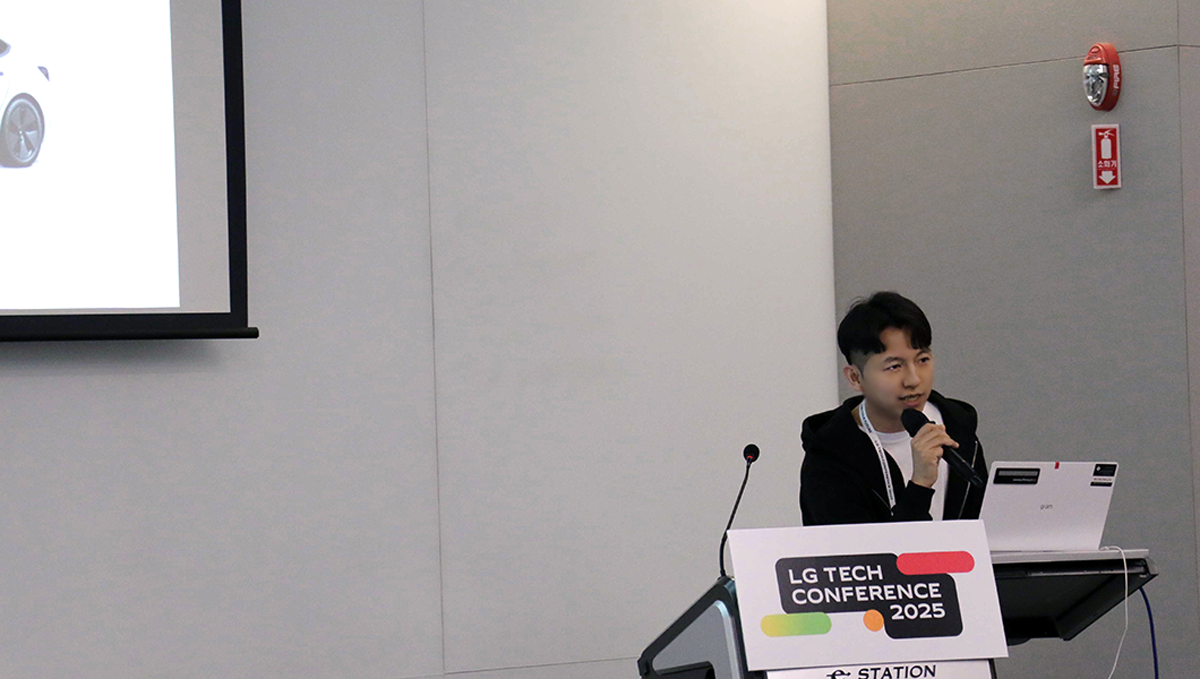
While advanced materials and technologies are important, customers ultimately want to know whether the battery cells will operate reliably and remain free of issues. LG Energy Solution leverages machine-learning methods (ML methods) built on 20 years of accumulated experimental data and expertise to diagnose cell conditions and even predict their future performance. With these methods, the company is now able to provide clear, data-driven answers to the customers’ question: “Are these cells really okay?”
The company is maximizing efficiency across the entire battery development process by introducing automation technologies. Rather than manually organizing the vast amounts of data generated from numerous experiments with the four core components, data collection and classification are now performed by automated systems. This shift has streamlined researchers’ workflows.
Leveraging its accumulated experience, technological expertise, and an ingrained drive for innovation, LG Energy Solution is leading technological innovation across the entire energy cycle from storage and transport to reuse. In line with our new vision, “Empower Every Possibility,” we are committed to awakening the world and bringing a better future with energy through continued research and bold challenges.
- Doping: Incorporation of a minimal quantity of another metal element into the cathode’s crystal structure ↩︎
- Phase transition: A change in the crystal structure of a substance under specific conditions, causing performance degradation or safety issues ↩︎
- Shut-down: A feature that automatically shuts down the battery’s operation in the event of an internal fault ↩︎
- Short circuit between electrodes: Direct contact between the cathode and anode inside the battery, overriding the normal current path and resulting in direct connection between the two ↩︎
- PFAS (per- and polyfluoroalkyl substances): A Group of synthetic chemicals that accumulate, instead of breaking down over time ↩︎
- MI (Materials Informatics): Research field that applies computer science and artificial intelligence to materials science ↩︎